When Doug Robertson, director of engineering at Clippard Inc. — a community-oriented company near Cincinnati — and his team initially approached AweSim, they were simply looking for help to segue their company into the world of high performance computing (HPC) modeling and simulation. What Robertson and the Clippard team wanted was simply to predict the performance of a spring in one of their electromagnetic proportional valves. After all, when your business is manufacturing valves, predictable and controlled fluid flow is essential.
What Robertson and Clippard didn’t expect was finding a flaw in the valve that nearly cost the company countless hours and dollars.
An unexpected flaw
Initially, AweSim contacted us at Kinetic Vision to provide detailed analyses of the valve. Ideally, the amount of fluid that flows through the valve is controlled by, and proportional to, the amount of electricity running to a solenoid coil that pulls on the spring. Early on, however, our test data on the prototype valve found a nonlinear trend for flow versus electric current. This was inconsistent with the flow analysis of the computer-aided design (CAD) files of the valve.
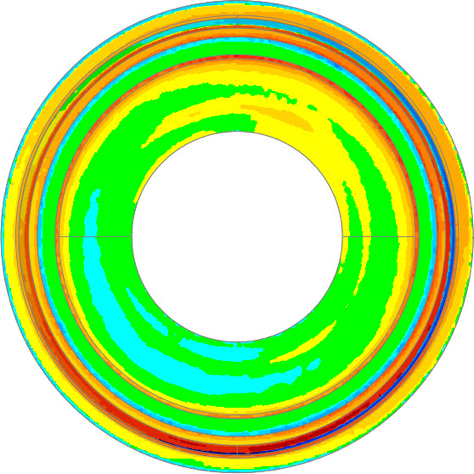
Computed tomography – not just for medical scans
We took a two-pronged approach to finding what was causing the discrepancies between the performance of the physical valve and the computer model. First, we performed a CT scan on the valve. CT, or computed tomography, is a technology that was initially developed for medical purposes and is now widely used across multiple industries to help design and develop products. A cone beam X-ray source sends radiation through an object, of which a 2D image is captured on a digital detector. This happens thousands of times as the object rotates a full 360 degrees, creating a three-dimensional model of the sample.
The depth, detail and the granularity of this information allow customers to really inspect their parts after they’re put together. We’re actually measuring these parts as they’re assembled so they can see what’s going on with the component in its operating state. By first performing an industrial CT scan of the assembled valve, we were able to compare the prototype with the computer model of the valve.
We then built a finite element model from the industrial CT scan. From this model, we found that the problem was not with the computer design of the valve, but in the manufacturing process Clippard was using.
It was the blend of those two tools – the nondestructive inspection from the CT scan and the finite element model – that really helped to solve their problem.
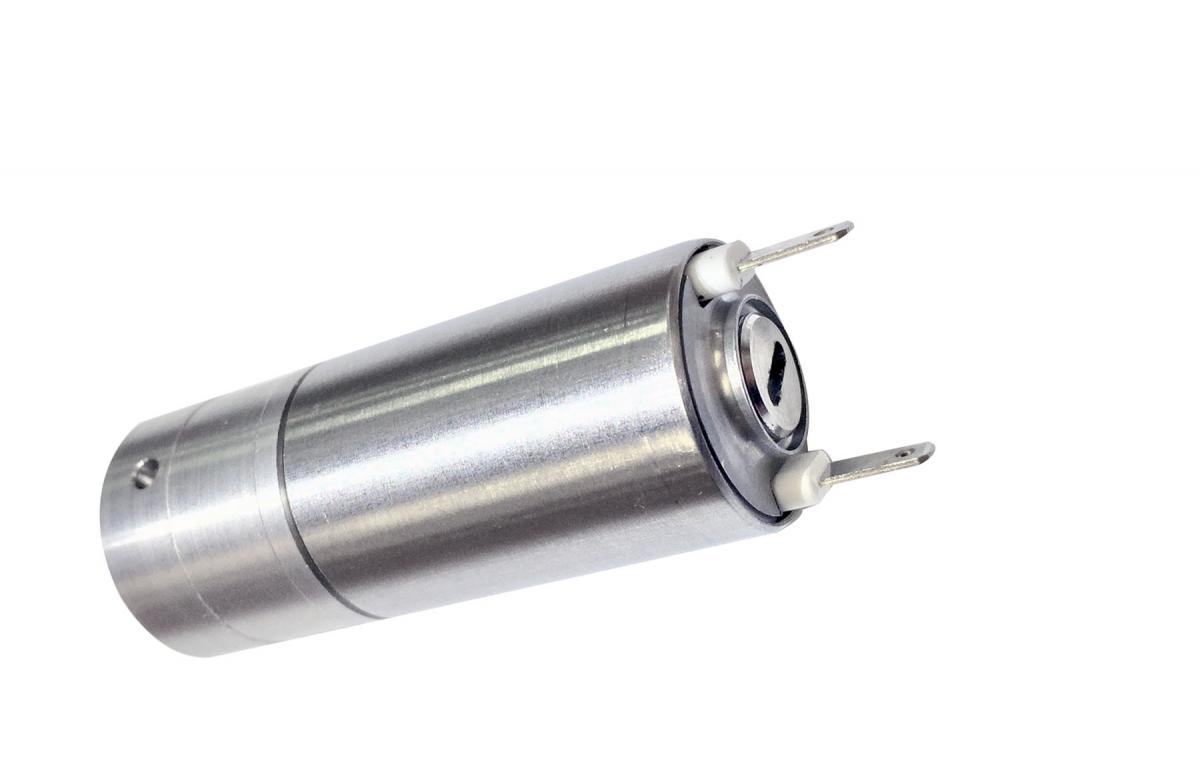
Having HPC resources, such as what is offered at the Ohio Supercomputer Center (OSC), at your disposal makes this type of methodology possible. We are solving high-fidelity finite element models directly generated from microCT data — it really helps enable that technique to even happen because the models have to be much more detailed.
Since the valve solution, Clippard has developed new methods to measure their material surface, improving processes from initial computational design to the finished product. As we’ve heard from clients over and over, modeling and simulation have saved the team valuable time and resources. Without Kinetic Vision’s intricately detailed analyses, scans and inspections through OSC resources, Clippard may not have been able to pinpoint what was causing the valve flow differential.